Anchored Reliability: Maintaining Vitality in Alaska's Mining and Oil Industry Pumps
Daisy Wick • April 20, 2024
Anchored Reliability: Maintaining Vitality in Alaska's Mining and Oil Industry Pumps
Nestled amidst Alaska's rugged terrain and icy waters lies a cornerstone of its economy—the mining and oil industry. Amidst this challenging environment, pumps stand as the unsung heroes, tirelessly extracting resources that fuel both local and global economies. Yet, behind their robust performance lies a critical truth: for Alaska's mining and oil industry to thrive, these pumps require meticulous maintenance and strategic replacement.
Alaska's mining and oil industry pumps serve as the lifeline of extraction processes, from dredging for gold in icy rivers to siphoning crude oil from remote drilling sites. However, the harsh conditions of the Alaskan wilderness pose unique challenges. Extreme temperatures, abrasive sediments, and corrosive substances test the resilience of these pumps, necessitating vigilant maintenance.
Regular maintenance is imperative to ensure the uninterrupted flow of resources in Alaska's mining and oil industry. Routine inspections, corrosion protection, and winterization measures are essential to combat the harsh elements and prevent costly downtime. Additionally, deploying innovative monitoring technologies, such as remote sensors and predictive analytics, can help anticipate potential issues and proactively address them before they escalate.
Despite diligent maintenance, the reality remains that Alaska's mining and oil industry pumps have a finite lifespan. Years of relentless operation in extreme conditions inevitably lead to wear and tear, necessitating timely replacement. Recognizing the signs of wear and strategically replacing pumps before they fail is essential to minimize disruptions and safeguard against production losses.
Timely pump replacement is not merely a matter of operational efficiency—it's a matter of survival for Alaska's mining and oil industry. The repercussions of pump failure extend beyond economic losses, impacting local communities and the environment. By investing in proactive replacement strategies and embracing technological advancements, such as high-efficiency pumps and corrosion-resistant materials, operators can enhance reliability, reduce downtime, and mitigate environmental risks.
In conclusion, Alaska's mining and oil industry pumps are the backbone of its economy, sustaining livelihoods and driving prosperity. However, their reliability hinges on meticulous maintenance and strategic replacement. By prioritizing proactive maintenance practices and embracing innovative solutions, Alaska's mining and oil industry can ensure the uninterrupted flow of resources, bolstering its resilience in the face of the rugged challenges of the Last Frontier.
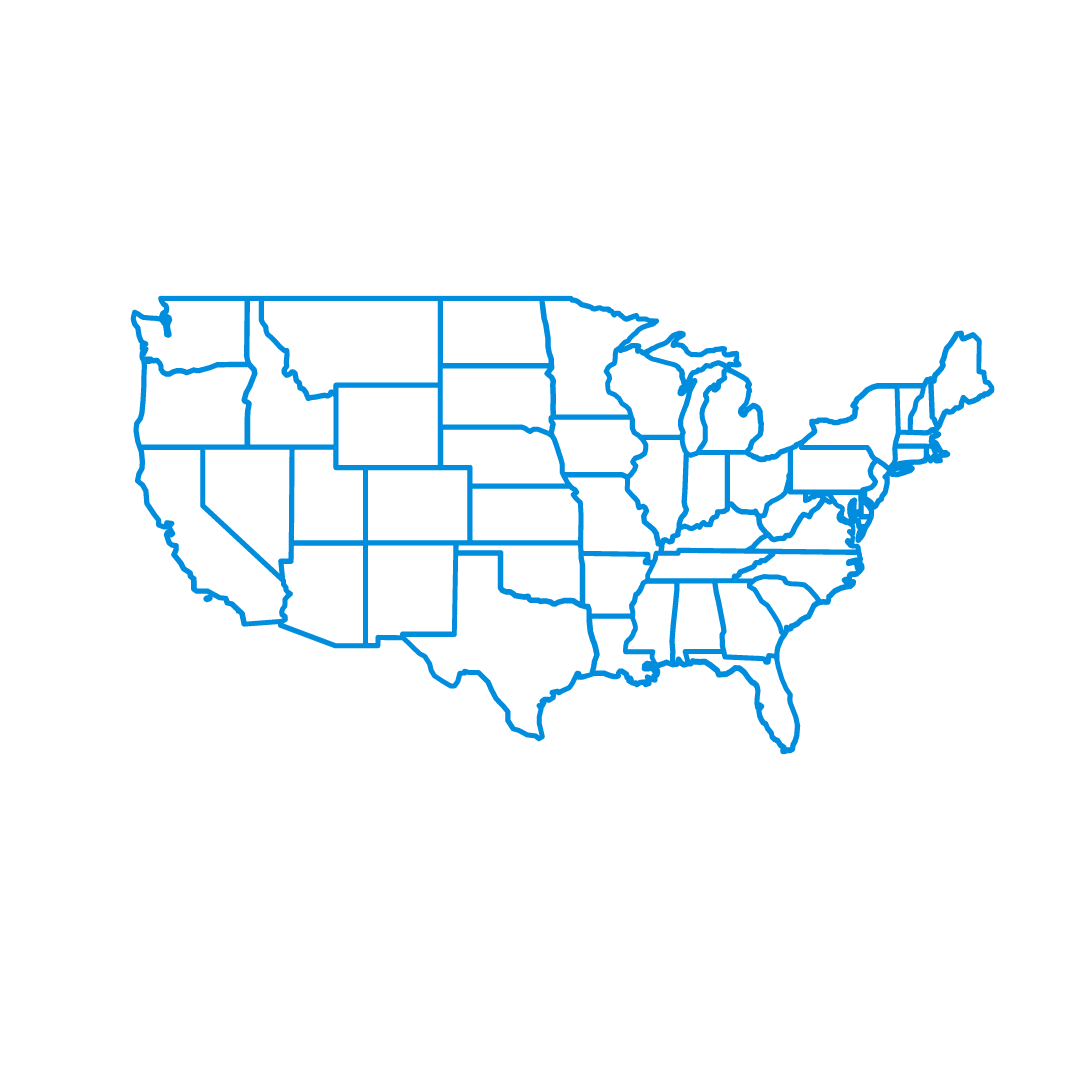
Industrial pumps are the silent workhorses powering some of the most critical sectors of the United States economy. From oil and gas production to water treatment and manufacturing, these essential machines ensure that fluids, from crude oil to wastewater, are moved efficiently and reliably. At Industrial Pumps of Alaska, we recognize the importance of these systems not just for our state but for the entire nation. The Backbone of Key Industries Several industries rely heavily on industrial pumps, making them indispensable to the U.S. economy: Oil and Gas: The oil and gas sector is a cornerstone of the U.S. economy, contributing significantly to GDP and employment. Pumps are essential in extracting crude oil, refining it into usable products, and transporting it through pipelines. Without industrial pumps, the energy sector would grind to a halt, affecting everything from transportation to manufacturing. Water and Wastewater Management: Clean water is a basic necessity, and pumps are crucial in both supplying water to homes and industries and in treating wastewater. Municipalities across the country depend on industrial pumps to maintain public health and safety by ensuring that clean water is available and wastewater is effectively managed. Manufacturing: From food processing to chemical production, the manufacturing sector relies on pumps to handle everything from raw materials to finished products. Pumps keep production lines running smoothly, impacting everything from the food we eat to the electronics we use daily. Agriculture: Agriculture is another critical sector that depends on industrial pumps. These pumps are used for irrigation, ensuring that crops receive the necessary water to grow, and for the transportation of fertilizers and pesticides. The efficiency of modern farming practices, and thus the stability of the nation's food supply, hinges on reliable pump systems. Mining: The mining industry is crucial for the extraction of minerals and resources needed for various sectors, including construction, technology, and manufacturing. Pumps play a key role in dewatering mines, transporting slurry, and processing ores, making them vital to the industry’s operations. Economic Impact The industries mentioned above are not just important for their output; they are also significant employers. Millions of Americans work in jobs related to oil and gas, manufacturing, agriculture, and more. The smooth operation of industrial pumps ensures that these industries continue to thrive, providing stable employment and supporting communities across the nation. In addition to employment, these industries generate substantial tax revenue, which funds public services and infrastructure. The U.S. economy is deeply interconnected, and the success of one sector often impacts others. For example, the availability of oil and gas affects transportation costs, which in turn influences the cost of goods and services across the economy. Innovation and Sustainability At Industrial Pumps of Alaska, we understand the importance of staying at the forefront of technological advancements. As industries evolve, so too must the pumps that serve them. Energy efficiency, sustainability, and reliability are key factors driving innovation in the pump industry. For example, as the country shifts towards more sustainable energy sources, such as wind and solar, the need for specialized pumps in these areas is growing. Furthermore, the emphasis on reducing water waste and improving water management systems is driving demand for advanced pump technologies that minimize environmental impact. Industrial pumps are the unsung heroes of the U.S. economy. They keep essential industries running, support millions of jobs, and contribute to the nation’s economic stability. At Industrial Pumps of Alaska, we take pride in being a part of this vital industry, ensuring that the pumps we provide are reliable, efficient, and ready to meet the demands of a dynamic economy. Whether it's in the frozen tundras of Alaska or the bustling factories of the Midwest, industrial pumps are at the heart of America's economic engine..
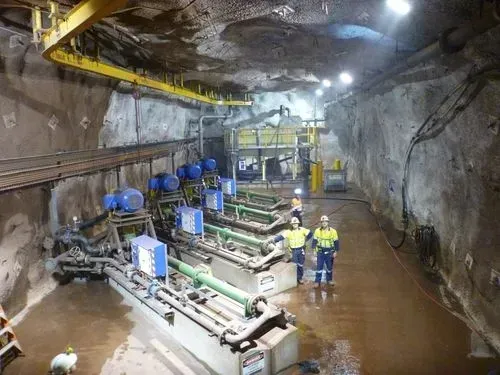
Welcome to Industrial Pumps of Alaska, where we have been proudly providing top-quality pump solutions for various industries across Alaska for years. Today, we are thrilled to announce an exciting expansion: we now offer our exceptional services to the entire Lower 48 states, with a special focus on the Pacific Northwest. A Legacy of Excellence At Industrial Pumps of Alaska, our reputation is built on a commitment to excellence. We understand the critical role that reliable pump systems play in industries ranging from oil and gas to agriculture and municipal water management. Our team of experts is dedicated to delivering the highest standards of service, ensuring that every pump system we install, maintain, or repair meets the rigorous demands of your operations. Expanding Our Horizons Our decision to expand into the Lower 48 states comes from a desire to bring our exceptional services and industry expertise to a broader audience. The Pacific Northwest, with its diverse industrial landscape and unique environmental challenges, presents an ideal region for us to showcase our capabilities. From Seattle's bustling ports to Portland's innovative manufacturing hubs, we are here to support your operations with the same dedication that has made us a trusted partner in Alaska. Services We Offer Pump Installation: Whether you need a new pump system for a manufacturing plant or an upgrade to an existing system, our team will ensure seamless installation with minimal disruption to your operations. Maintenance and Repair: Regular maintenance is crucial to the longevity and efficiency of your pump systems. Our skilled technicians are equipped to handle routine maintenance and urgent repairs, keeping your systems running smoothly. Consultation and Design: Every industry has unique requirements. Our consultation and design services ensure that you get a pump system tailored to your specific needs, enhancing productivity and reducing operational costs. Emergency Services: Pump failures can happen at any time, and we understand the urgency of getting your systems back online. Our 24/7 emergency services are designed to provide quick, effective solutions when you need them most. Why Choose Industrial Pumps of Alaska? Expertise: Our team comprises experienced professionals with extensive knowledge of various pump systems and applications. Quality: We use only the highest quality parts and equipment to ensure durability and reliability. Customer Focus: Your satisfaction is our priority. We work closely with you to understand your needs and deliver solutions that exceed expectations. Sustainability: We are committed to environmentally responsible practices, helping you achieve sustainability goals with energy-efficient pump systems. Get in Touch We are excited to bring our services to the Lower 48 states and look forward to becoming your trusted partner in the Pacific Northwest. For more information about our services or to schedule a consultation, please contact us at: Facebook: Industrial Pumps of Alaska Join us as we embark on this exciting new chapter, bringing the reliability and excellence of Industrial Pumps of Alaska to the Lower 48 states. Together, we can power the industries that drive our economy forward. Thank you for your continued support. Sincerely, The Team at Industrial Pumps of Alaska
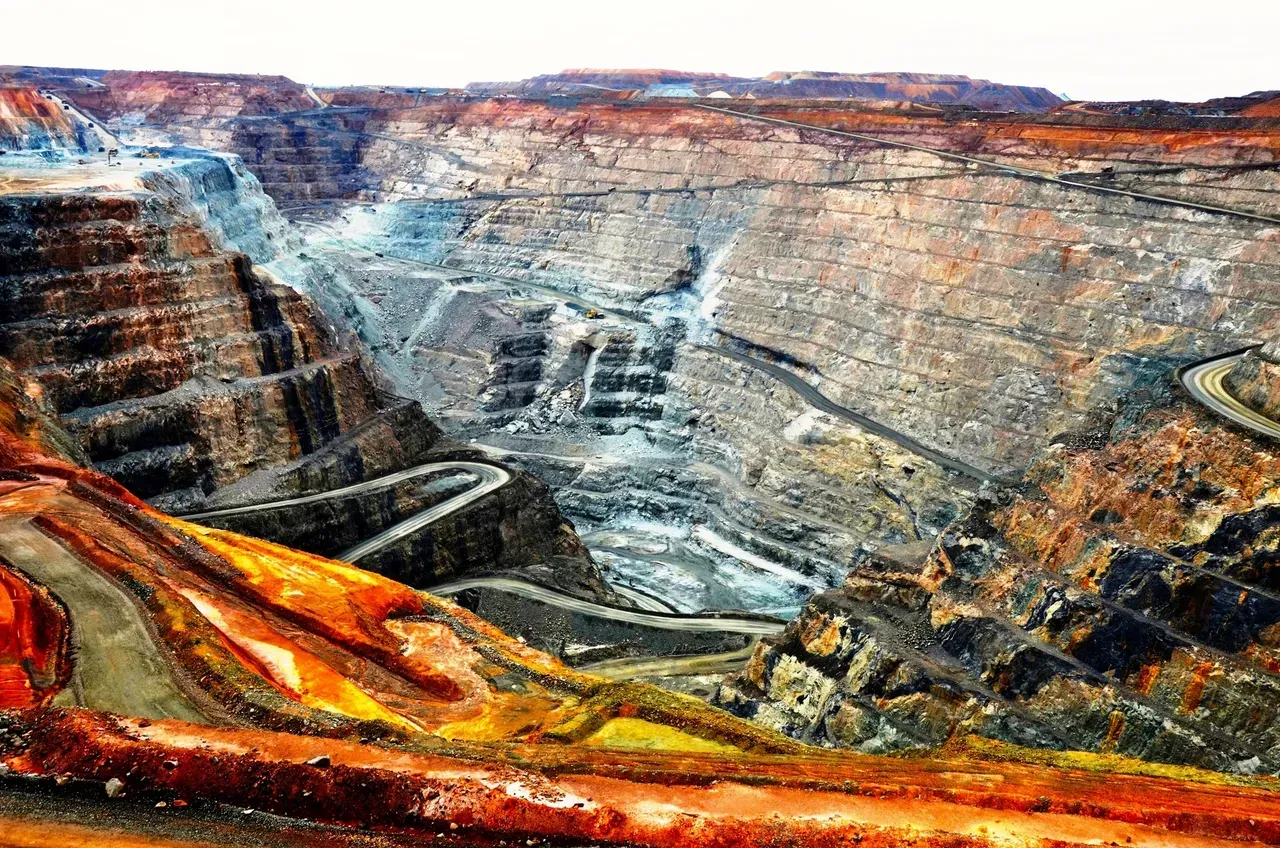
Alaska's harsh climate and remote locations pose significant challenges for industries that rely on mechanical pumps. The frigid temperatures and demanding conditions require pumps that can perform reliably without frequent maintenance or failure. In this blog, we'll explore which pumps are best suited for cold weather performance and how they meet the needs of various Alaskan industries. Gear Pumps: Precision and Durability in Cold Climates 1. Cold Weather Performance: Gear pumps are known for their high efficiency and precision, which remain consistent even in cold temperatures. Their robust construction and fewer moving parts make them less susceptible to temperature-related issues. 2. Industrial Applications: Oil and Gas: Gear pumps are widely used for transferring lubricating oils, fuels, and other viscous fluids. Their ability to maintain a steady flow rate is crucial for hydraulic systems and chemical processing. Chemical Processing: In industries dealing with chemicals, gear pumps ensure the precise handling of various fluids without performance degradation. 3. Advantages: Durability: Built to withstand high pressures and tough environments, gear pumps offer long-lasting performance. Efficiency: They provide a consistent flow rate, which is essential for operations requiring precise fluid control. Diaphragm Pumps: Versatility and Robustness in Extreme Conditions 1. Cold Weather Performance: Diaphragm pumps excel in cold weather due to their ability to self-prime and run dry without damage. This makes them highly reliable in remote and harsh conditions where maintenance resources are limited. 2. Industrial Applications: Water Treatment: Diaphragm pumps are used in dewatering, water treatment plants, and handling wastewater, ensuring reliable performance in freezing temperatures. Mining: The mining industry in Alaska benefits from diaphragm pumps for slurry and sludge handling, where the ability to handle abrasive materials is crucial. 3. Advantages: Self-Priming Capability: These pumps do not require manual priming, making them convenient for remote locations. Solids Handling: Capable of pumping slurries and fluids with high solid content without clogging. Corrosion Resistance: Suitable for handling aggressive chemicals and corrosive substances. Peristaltic Pumps: Reliable and Low Maintenance 1. Cold Weather Performance: Peristaltic pumps, with their sealed design and minimal moving parts, offer excellent reliability in cold weather. The pump’s tubing can be made from materials that remain flexible in low temperatures. 2. Industrial Applications: Agriculture: Used for precise dosing of fertilizers and chemicals, ensuring efficient operation even in cold climates. Food and Beverage: Ideal for hygienic applications where contamination must be avoided, functioning well in low-temperature environments. 3. Advantages: Low Maintenance: With no valves, seals, or glands, these pumps require minimal maintenance. Contamination-Free: The fluid only contacts the tubing, reducing the risk of contamination and making them suitable for sensitive applications. Centrifugal Pumps: Adaptability with Proper Precautions 1. Cold Weather Performance: Centrifugal pumps can be adapted for cold weather use with proper precautions, such as insulation and heat tracing to prevent freezing. 2. Industrial Applications: Water Supply: Commonly used in water distribution systems, centrifugal pumps can be adapted to operate efficiently in cold climates with the right modifications. Construction: Used for dewatering and other fluid transfer tasks on construction sites, provided they are adequately protected from freezing. 3. Advantages: High Flow Rates: Centrifugal pumps are capable of moving large volumes of fluid efficiently. Versatility: Suitable for a wide range of applications, including water supply and industrial fluid transfer. Conclusion When selecting pumps for use in Alaska's cold weather and demanding industry climates, it's essential to consider the specific needs of each application. Gear pumps offer precision and durability, making them ideal for the oil and gas sector. Diaphragm pumps provide versatility and robustness, perfect for water treatment and mining. Peristaltic pumps ensure reliable, low-maintenance operation for agriculture and food industries. Lastly, centrifugal pumps can be adapted for cold weather with proper precautions, serving various purposes from water supply to construction. Understanding these options and their unique benefits ensures that Alaskan industries can maintain efficient and reliable operations despite the challenging conditions.
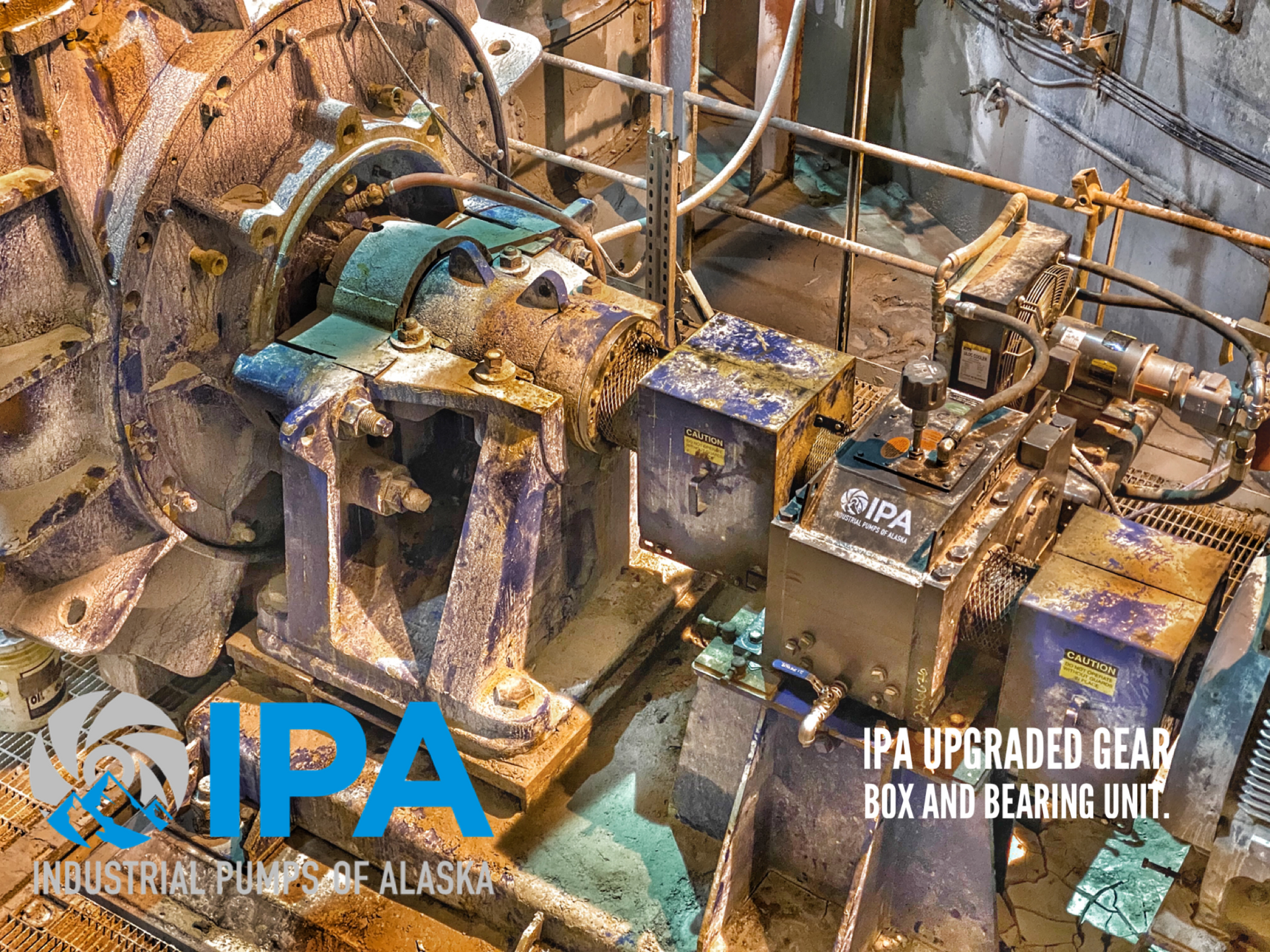
Alaska, with its vast wilderness, extreme climate, and remote locations, presents unique challenges for industries such as oil and gas, mining, and agriculture. These sectors rely heavily on mechanical pumps to transfer fluids, maintain operations, and ensure efficiency. Among the numerous types of pumps available, gear pumps and diaphragm pumps are particularly noteworthy for their distinct functionalities and advantages. In this blog, we'll delve into the differences between these two types of mechanical pumps and explore why they are essential in the Alaskan context. Gear Pumps: Precision and Reliability 1. How They Work: Gear pumps operate on a simple yet effective principle. They consist of two interlocking gears—one driving and one driven—encased in a housing. As the gears rotate, fluid is trapped in the spaces between the gear teeth and the casing. This trapped fluid is then moved from the inlet to the outlet, creating a steady, pulseless flow. 2. Applications in Alaska: In Alaska, gear pumps are widely used in the oil and gas industry for transferring lubricating oils, fuels, and other viscous fluids. Their precision and reliability make them ideal for applications where consistent flow and pressure are critical, such as in hydraulic systems and chemical processing. 3. Advantages: High Efficiency: Gear pumps maintain a consistent flow rate, making them highly efficient for various applications. Durability: With fewer moving parts and robust construction, gear pumps can handle high-pressure operations and are less prone to wear and tear. Versatility: They can handle a wide range of viscosities, making them suitable for different types of fluids. 4. Limitations: Not Self-Priming: Gear pumps need to be primed before operation, which can be a limitation in some scenarios. Susceptible to Abrasive Wear: Fluids with particulates can cause wear and damage to the gears over time. Diaphragm Pumps: Versatility and Robustness 1. How They Work: Diaphragm pumps utilize a flexible diaphragm driven by a mechanical, hydraulic, or pneumatic actuator. As the diaphragm moves back and forth, it creates a vacuum that draws fluid into the pump chamber. On the return stroke, the fluid is pushed out of the chamber through an outlet valve, ensuring a controlled and consistent flow. 2. Applications in Alaska: Diaphragm pumps are highly valued in Alaska for their versatility and ability to handle challenging conditions. They are commonly used in water treatment, dewatering, and handling corrosive or abrasive fluids. Their self-priming capability and ability to run dry without damage make them suitable for remote locations where maintenance is difficult. 3. Advantages: Self-Priming: Diaphragm pumps can start pumping without needing to be primed, making them highly convenient. Handles Solids: These pumps can handle slurries, sludge, and fluids with high solid content without clogging. Corrosion Resistance: Diaphragm pumps can be made from various materials, making them suitable for pumping aggressive chemicals and corrosive substances. 4. Limitations: Lower Flow Rates: Compared to gear pumps, diaphragm pumps typically have lower flow rates and are less efficient for high-volume applications. Pulsating Flow: The nature of diaphragm movement can create a pulsating flow, which may require additional measures to smooth out in certain applications. Choosing the Right Pump for Alaska When selecting a mechanical pump for use in Alaska, several factors should be considered: Fluid Characteristics: Consider the viscosity, abrasiveness, and corrosiveness of the fluid being pumped. Operational Environment: Assess the ambient temperature, remote location, and the availability of maintenance resources. Application Requirements: Determine the required flow rate, pressure, and whether the pump needs to be self-priming or capable of handling solids. In summary, both gear pumps and diaphragm pumps have unique attributes that make them suitable for different applications in Alaska. Gear pumps excel in precision and efficiency, making them ideal for handling lubricating oils and fuels. Diaphragm pumps, on the other hand, offer versatility and robustness, making them perfect for dewatering, water treatment, and handling challenging fluids. Understanding the specific needs of your application will help you make an informed decision and ensure reliable and efficient operations in Alaska's demanding environment.
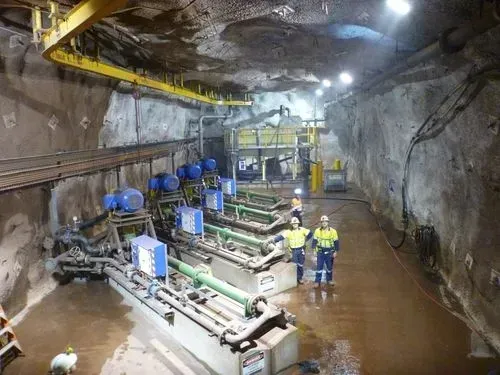
In the complex web of industries reliant on pumps, from manufacturing to oil extraction, the heartbeat of operations often lies within these mechanical workhorses. Yet, beyond their physical presence, lies a crucial factor that can make or break efficiency, productivity, and ultimately, profitability—choosing the right partner for industrial pump maintenance and sales. Here’s why this decision matters more than you might think. First and foremost, expertise matters. Industrial pumps come in various shapes, sizes, and complexities, each tailored to specific applications and industries. Entrusting maintenance and sales to a partner with deep knowledge and experience ensures that your pumps are in capable hands. From routine servicing to troubleshooting complex issues, an experienced provider can offer insights and solutions that maximize pump performance and longevity. Moreover, reliability is paramount. Downtime in industrial operations can spell disaster, leading to production delays, missed deadlines, and significant financial losses. Partnering with a reliable maintenance and sales provider means having access to prompt assistance when issues arise. Whether it's emergency repairs or swift delivery of replacement parts, a dependable partner ensures minimal disruption to your operations, keeping downtime at bay. But it’s not just about fixing problems—it’s about preventing them in the first place. Proactive maintenance plays a pivotal role in prolonging the lifespan of industrial pumps and optimizing their performance. A trusted partner will offer tailored maintenance plans, incorporating preventive measures such as regular inspections, lubrication, and component replacements. By addressing potential issues before they escalate, proactive maintenance not only minimizes downtime but also reduces long-term operational costs. Furthermore, quality matters. When it comes to purchasing new pumps or replacement parts, the quality of the products and services offered by your partner can significantly impact overall performance and reliability. Opting for subpar equipment or components may save costs upfront, but it can lead to inferior performance, frequent breakdowns, and ultimately, higher expenses in the long run. Choosing a partner that prioritizes quality ensures that you’re investing in products and services that deliver lasting value. Additionally, flexibility and customization are key considerations. Industrial operations vary widely in their requirements and constraints, from space limitations to environmental factors. A partner that offers flexible solutions and customization options can tailor their offerings to meet your specific needs, ensuring optimal compatibility and performance in your unique operational environment. Last but not least, reputation speaks volumes. Word-of-mouth recommendations and testimonials from satisfied customers are invaluable indicators of a partner's reliability, expertise, and commitment to customer satisfaction. Choosing a partner with a stellar reputation in the industry provides added assurance that you’re making the right decision for your pump maintenance and sales needs. In conclusion, the choice of who you entrust with your industrial pump maintenance and sales is not a decision to be taken lightly. From expertise and reliability to quality and reputation, numerous factors come into play. By selecting a partner that embodies these qualities, you’re not just investing in pumps—you’re investing in the seamless operation, efficiency, and success of your entire industrial ecosystem.
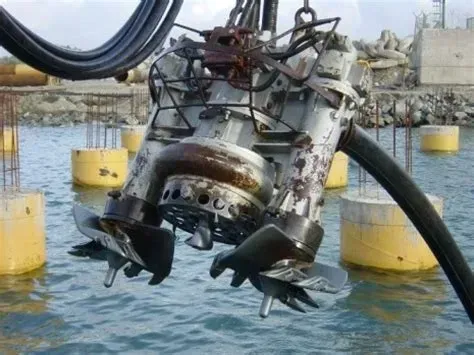
Dewatering pumps are typically high speed, higher pressure pumps (3600 RPM 2pole units). In typical dewatering applications the equipment runs per design and stays submerged in fairly clean cool water. In that environment, they run very good and will last a long time. The great thing about "slurry" submersible pumps in comparison to standard dewatering pumps is that they spin at low speed (600,800,1200,1800 RPM) and generate much less mechanical issues. The problem is that they are not as efficient, and are not capable of high discharge pressures the dewatering pumps are (there are many difference not listed...this is just a few). A lot of mines try...and do utilize the higher pressure producing dewatering pumps. They do so because they need the higher pressure (or prefer it) to pump out sumps without a charge to booster pump set-ups. Without the proper selection, well maintained sumps, and decent controls, these dewatering pumps can and will cause major issues in mine dewatering and can create very short periods between MTBF. In one mine, I took over the dewatering pump repair. It was a mess, about 1.2Million a year in pump repair. Some of the pumps were coming in and out of the mine on a bi-weekly basis. I believe there were 12 8HP pumps (only part of the fleet)...one month, those twelve pumps were repaired 19 times. Obviously, the issues weren't just sump and operation related, the shop previously rebuilding the equipment was not doing a very sub-standard job. After the pumps were properly rebuilt, and the equipment was properly installed. This included controls, and new transport techniques we limited the 8HP pumps to an average of two per month. The failure modes common with dewatering pumps in hard rock mining range from (in my experience) damage during transport, transient voltage spikes, damaged cords, incorrect pump hydraulics, plugged suctions, etc...all very common. However, the two most common failures have to be failed mechanical seals (which without thermal controls leads the stators burning out), and plugged suctions. This is due to the sumps solids falling out of entrainment and ultimately building up until the sump bottom. The fallout plugs the pump and causes it to either go out on amps, or get hot and fail the mechanical seals, and then the motor. Slurry submersible pumps are much more forgiving and can handle running with a plugged suction, or loss of submergence for much longer. The high speed generated by the dewatering pumps creates exponential heat build-up, this fails the mechanical seals (and wet end components) much faster. The issue is lack of pressure. I think the solution is to utilize proper controls. Make sure the sumps have a pump saver or some kind of equipment to monitor the pumps amperage and control the sumps voltage variants. It is important to educate the underground miners on the sensitivity of the pumps, and how they are precision equipment that function with a purpose. If that doesn't work, put in a Hevvy submersible...and do a charge/booster set up if need be. However, if nothing is done to educate the mine on the dewatering pumps they will cause an enormous issue. There is much more I could add to this blog...but its time for bed. If anyone has any questions please give me a call or an email. Thanks, Houston